Destylacja rozpuszczalników to proces, który polega na oddzieleniu substancji na podstawie różnicy w ich temperaturach wrzenia. W praktyce oznacza to, że ciecz, która ma niższą temperaturę wrzenia, odparowuje jako pierwsza, a następnie skrapla się w chłodnicy, tworząc czystszy produkt. Proces ten jest szeroko stosowany w przemyśle chemicznym oraz farmaceutycznym do oczyszczania rozpuszczalników, które mogą być zanieczyszczone innymi substancjami. Destylacja może być przeprowadzana w różnych warunkach, w tym pod ciśnieniem atmosferycznym lub w warunkach próżniowych, co pozwala na obniżenie temperatury wrzenia niektórych substancji. W zależności od zastosowania można wyróżnić kilka typów destylacji, takich jak destylacja prosta, frakcyjna czy azeotropowa. Każda z tych metod ma swoje specyficzne zastosowania i zalety, które są dostosowane do potrzeb przemysłowych oraz laboratoryjnych.
Jakie są zastosowania destylacji rozpuszczalników w przemyśle
Zastosowanie destylacji rozpuszczalników w przemyśle jest niezwykle szerokie i obejmuje wiele dziedzin. W przemyśle chemicznym destylacja jest kluczowym procesem wykorzystywanym do oczyszczania surowców oraz produktów końcowych. Na przykład, w produkcji alkoholi etylowych destylacja pozwala na oddzielenie etanolu od innych składników fermentacyjnych. W przemyśle farmaceutycznym proces ten jest niezbędny do uzyskiwania czystych substancji czynnych, które są później wykorzystywane w lekach. Dodatkowo destylacja znajduje zastosowanie w produkcji olejków eterycznych, gdzie pozwala na wydobycie aromatycznych składników roślinnych. W branży petrochemicznej proces ten jest stosowany do separacji różnych frakcji ropy naftowej, co umożliwia uzyskanie paliw oraz innych produktów chemicznych. Również w laboratoriach badawczych destylacja jest często wykorzystywana do oczyszczania rozpuszczalników przed ich użyciem w eksperymentach.
Jakie są różnice między różnymi metodami destylacji rozpuszczalników
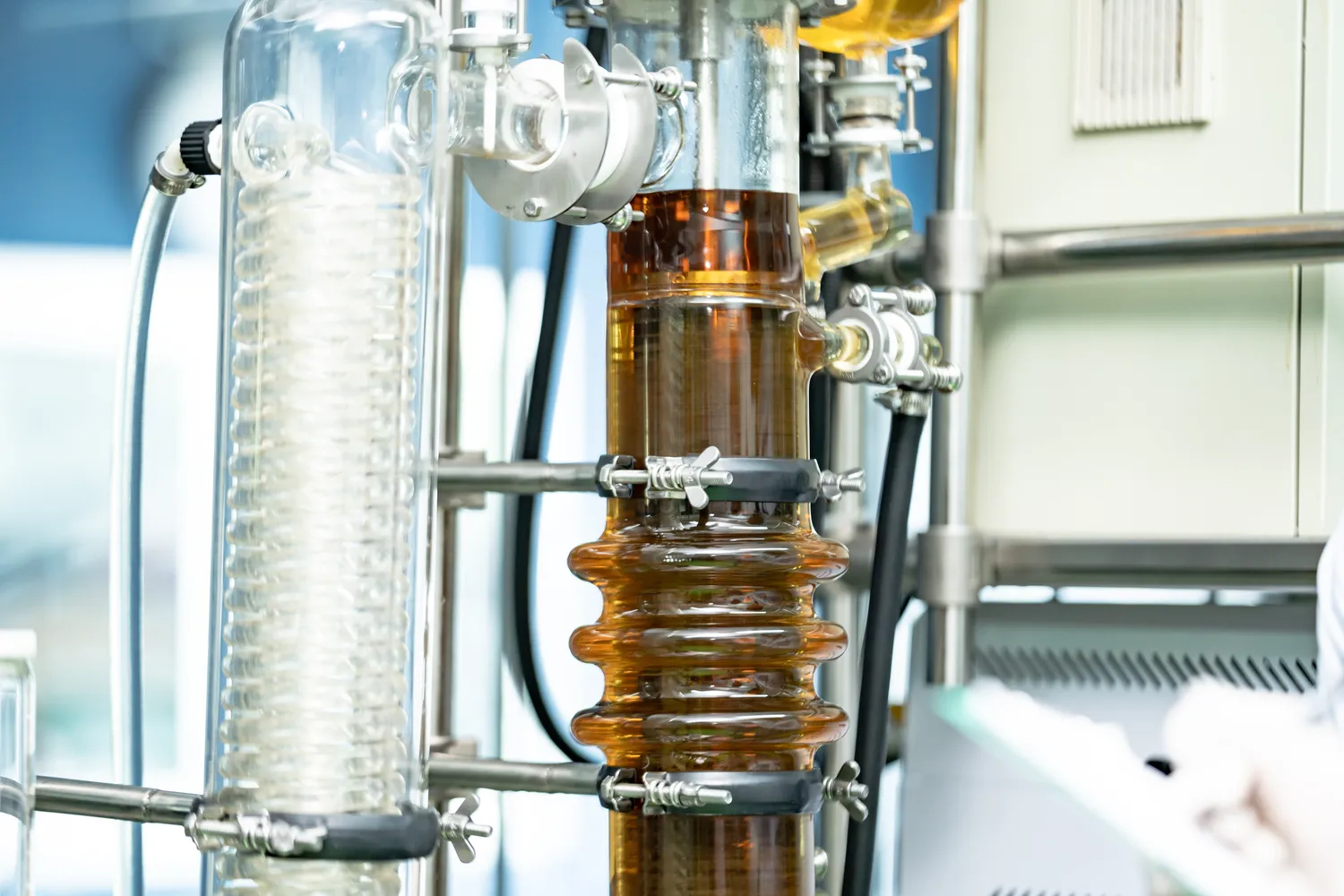
Różne metody destylacji rozpuszczalników mają swoje unikalne cechy i zastosowania, co sprawia, że wybór odpowiedniej metody zależy od specyfiki procesu oraz rodzaju substancji. Destylacja prosta jest najprostszą formą tego procesu i polega na jednorazowym odparowaniu cieczy i jej skropleniu. Jest skuteczna przy separacji substancji o znacznie różniących się temperaturach wrzenia. Z kolei destylacja frakcyjna jest bardziej zaawansowaną metodą, która wykorzystuje kolumny frakcyjne do wielokrotnego skraplania i odparowywania cieczy, co pozwala na dokładniejsze oddzielenie składników o zbliżonych temperaturach wrzenia. Metoda ta jest szczególnie przydatna w przypadku złożonych mieszanin chemicznych. Destylacja azeotropowa natomiast dotyczy mieszanin, które tworzą azeotropy – substancje o stałym składzie chemicznym podczas parowania. W takich przypadkach konieczne może być dodanie innego rozpuszczalnika lub zmiana warunków procesu, aby uzyskać pożądany efekt separacji.
Jakie sprzęty są potrzebne do przeprowadzenia destylacji rozpuszczalników
Aby przeprowadzić proces destylacji rozpuszczalników, niezbędny jest odpowiedni sprzęt laboratoryjny lub przemysłowy dostosowany do specyfiki danego procesu. Podstawowym elementem wyposażenia jest aparat destylacyjny, który składa się z naczynia do podgrzewania cieczy oraz systemu chłodzenia pary. Naczynie to zazwyczaj wykonane jest ze szkła lub stali nierdzewnej i musi być odporne na wysokie temperatury oraz działanie chemikaliów. Chłodnica służy do skraplania pary i powinna być efektywna, aby zapewnić maksymalne odzyskanie produktu. Dodatkowo istotne są termometry oraz manometry umożliwiające kontrolę temperatury i ciśnienia podczas procesu. W przypadku bardziej zaawansowanych metod destylacji frakcyjnej konieczne mogą być kolumny frakcyjne oraz dodatkowe urządzenia takie jak zbiorniki buforowe czy pompy próżniowe. Ważnym aspektem jest również bezpieczeństwo pracy z substancjami chemicznymi, dlatego warto zaopatrzyć się w odpowiednie środki ochrony osobistej oraz systemy wentylacyjne.
Jakie są kluczowe czynniki wpływające na efektywność destylacji rozpuszczalników
Efektywność procesu destylacji rozpuszczalników zależy od wielu czynników, które mogą znacząco wpłynąć na jakość i ilość uzyskanego produktu. Jednym z najważniejszych elementów jest temperatura wrzenia substancji, która determinuje moment ich odparowania. Właściwe ustawienie temperatury jest kluczowe, ponieważ zbyt wysoka temperatura może prowadzić do degradacji substancji, a zbyt niska może skutkować niepełnym oddzieleniem składników. Kolejnym czynnikiem jest ciśnienie, które wpływa na temperaturę wrzenia cieczy. W przypadku destylacji próżniowej, obniżenie ciśnienia pozwala na przeprowadzenie procesu w niższych temperaturach, co jest korzystne dla wrażliwych substancji chemicznych. Również czas trwania destylacji ma znaczenie; zbyt krótki czas może skutkować niepełnym oddzieleniem składników, podczas gdy zbyt długi czas może prowadzić do strat materiałowych. Dodatkowo, jakość używanych materiałów oraz sprzętu ma wpływ na efektywność procesu. Użycie odpowiednich rozpuszczalników oraz dokładne przygotowanie aparatury mogą znacznie zwiększyć wydajność destylacji.
Jakie są najczęstsze problemy podczas destylacji rozpuszczalników
Podczas przeprowadzania destylacji rozpuszczalników mogą wystąpić różnorodne problemy, które mogą wpłynąć na jakość i wydajność procesu. Jednym z najczęstszych problemów jest tworzenie się azeotropów, które mogą utrudniać separację składników o podobnych temperaturach wrzenia. Azeotropy to mieszaniny o stałym składzie chemicznym, które parują w określonym stosunku, co sprawia, że trudno je oddzielić za pomocą standardowej destylacji. Innym problemem mogą być zanieczyszczenia w surowcach, które mogą wpływać na końcowy produkt i jego czystość. Zanieczyszczenia te mogą pochodzić z różnych źródeł, takich jak nieodpowiednie przechowywanie czy kontakt z innymi substancjami chemicznymi. Dodatkowo niewłaściwe ustawienia temperatury i ciśnienia mogą prowadzić do nieefektywnej separacji składników lub nawet do ich degradacji. W przypadku destylacji frakcyjnej mogą wystąpić problemy związane z niewłaściwym działaniem kolumny frakcyjnej, co może skutkować niską jakością uzyskiwanego produktu.
Jakie są różnice między destylacją a innymi metodami separacji
Destylacja to jedna z wielu metod separacji substancji chemicznych, ale różni się od innych technik pod względem zasad działania i zastosowań. Na przykład ekstrakcja to proces polegający na oddzieleniu składników na podstawie ich rozpuszczalności w różnych rozpuszczalnikach. Ekstrakcja jest często stosowana w przypadkach, gdy substancje mają różne właściwości chemiczne i fizyczne, co umożliwia ich selektywne oddzielenie bez potrzeby podgrzewania. Z kolei chromatografia to technika separacyjna oparta na różnicach w przyleganiu substancji do fazy stacjonarnej i ruchomej. Chromatografia jest szczególnie przydatna w analizach jakościowych i ilościowych oraz w badaniach laboratoryjnych. W przeciwieństwie do tych metod, destylacja koncentruje się głównie na różnicach w temperaturze wrzenia substancji, co czyni ją bardziej odpowiednią do separacji cieczy o podobnych właściwościach fizycznych. Każda z tych metod ma swoje zalety i ograniczenia; wybór odpowiedniej techniki zależy od specyfiki zadania oraz rodzaju substancji do oddzielenia.
Jakie są nowoczesne technologie stosowane w destylacji rozpuszczalników
Nowoczesne technologie stosowane w destylacji rozpuszczalników ewoluują wraz z postępem technologicznym i rosnącymi wymaganiami przemysłowymi. Jednym z najnowszych trendów jest automatyzacja procesów destylacyjnych, która pozwala na zwiększenie precyzji oraz efektywności operacji. Dzięki zastosowaniu zaawansowanych systemów monitorowania i kontroli możliwe jest ciągłe śledzenie parametrów procesu oraz automatyczne dostosowywanie warunków pracy do zmieniających się potrzeb produkcji. Ponadto rozwój technologii membranowych otworzył nowe możliwości dla separacji cieczy; membrany mogą być wykorzystywane do usuwania określonych składników bez konieczności podgrzewania całej mieszaniny. Innowacyjne podejścia obejmują również wykorzystanie nanotechnologii w procesach oczyszczania oraz zastosowanie nowych materiałów konstrukcyjnych dla aparatów destylacyjnych, co zwiększa ich trwałość i efektywność energetyczną. Również rozwój technologii próżniowej umożliwia przeprowadzanie procesów w niższych temperaturach, co jest korzystne dla wielu wrażliwych substancji chemicznych.
Jakie są przepisy dotyczące bezpieczeństwa przy destylacji rozpuszczalników
Bezpieczeństwo podczas procesu destylacji rozpuszczalników jest kluczowym aspektem zarówno w laboratoriach badawczych, jak i w zakładach przemysłowych. Przepisy dotyczące bezpieczeństwa nakładają obowiązek stosowania odpowiednich środków ochrony osobistej dla pracowników zajmujących się tym procesem. Należy zapewnić użycie okularów ochronnych, rękawic oraz odzieży odpornych na działanie chemikaliów. Ważnym elementem bezpieczeństwa jest również odpowiednia wentylacja pomieszczeń roboczych; wiele rozpuszczalników ma lotne opary, które mogą być szkodliwe dla zdrowia przy dłuższym narażeniu. Dodatkowo należy przestrzegać zasad dotyczących przechowywania substancji chemicznych oraz ich transportu wewnętrznego; wszelkie materiały łatwopalne powinny być składowane w odpowiednich pojemnikach zabezpieczających przed wybuchem lub pożarem. Warto także regularnie przeprowadzać szkolenia dla pracowników dotyczące procedur awaryjnych oraz postępowania w przypadku wycieku czy innego incydentu związane z substancjami chemicznymi.
Jakie są przyszłe kierunki badań nad destylacją rozpuszczalników
Przyszłe kierunki badań nad destylacją rozpuszczalników koncentrują się na poszukiwaniu bardziej efektywnych i ekologicznych metod separacji substancji chemicznych. W obliczu rosnącej potrzeby ograniczenia zużycia energii oraz minimalizacji wpływu procesów przemysłowych na środowisko naukowcy badają nowe technologie i materiały, które mogłyby zastąpić tradycyjne metody destylacyjne. Jednym z obszarów badań są innowacyjne systemy wykorzystujące energię słoneczną lub inne odnawialne źródła energii do przeprowadzania procesów separacyjnych. Również rozwój nanomateriałów otwiera nowe możliwości dla efektywniejszej filtracji i separacji cieczy poprzez zastosowanie nanostruktur o unikalnych właściwościach fizykochemicznych. Badania nad zastosowaniem sztucznej inteligencji i uczenia maszynowego w optymalizacji procesów destylacyjnych również stają się coraz bardziej popularne; algorytmy te mogą pomóc w przewidywaniu zachowań mieszanin chemicznych oraz dostosowywaniu parametrów procesu w czasie rzeczywistym.