Budowa maszyn pneumatycznych opiera się na kilku kluczowych elementach, które współpracują ze sobą, aby zapewnić efektywne działanie systemu. Wśród najważniejszych komponentów można wymienić sprężarki, które są odpowiedzialne za generowanie sprężonego powietrza. Sprężarki mogą mieć różne konstrukcje, w tym tłokowe, śrubowe czy wirnikowe, a ich wybór zależy od specyfiki zastosowania. Kolejnym istotnym elementem są zbiorniki na sprężone powietrze, które gromadzą powietrze w celu stabilizacji ciśnienia w systemie. Rury i przewody pneumatyczne transportują sprężone powietrze do poszczególnych urządzeń wykonawczych, takich jak siłowniki i zawory. Siłowniki pneumatyczne przekształcają energię sprężonego powietrza w ruch mechaniczny, co pozwala na wykonywanie różnych zadań, od prostych ruchów liniowych po skomplikowane procesy automatyzacji. Zawory sterujące regulują przepływ powietrza w systemie, co umożliwia precyzyjne zarządzanie ruchem i siłą działania maszyn.
Jakie są zalety używania maszyn pneumatycznych w przemyśle
Maszyny pneumatyczne zyskują na popularności w różnych gałęziach przemysłu dzięki swoim licznym zaletom. Jedną z głównych korzyści jest ich wysoka wydajność energetyczna. Systemy pneumatyczne potrafią szybko generować dużą moc przy stosunkowo niskim zużyciu energii, co przekłada się na oszczędności kosztów operacyjnych. Kolejnym atutem jest ich prostota konstrukcji oraz łatwość w obsłudze i konserwacji. W porównaniu do innych systemów napędowych, takich jak hydrauliczne czy elektryczne, maszyny pneumatyczne często wymagają mniej skomplikowanej infrastruktury oraz mają mniejsze ryzyko awarii mechanicznych. Dodatkowo, maszyny te charakteryzują się dużą elastycznością zastosowania – mogą być wykorzystywane w różnych procesach produkcyjnych, od pakowania po montaż. Ich zdolność do pracy w trudnych warunkach środowiskowych sprawia, że są idealnym rozwiązaniem w branżach takich jak przemysł spożywczy czy farmaceutyczny, gdzie czystość i bezpieczeństwo są kluczowe.
Jakie zastosowania mają maszyny pneumatyczne w różnych branżach
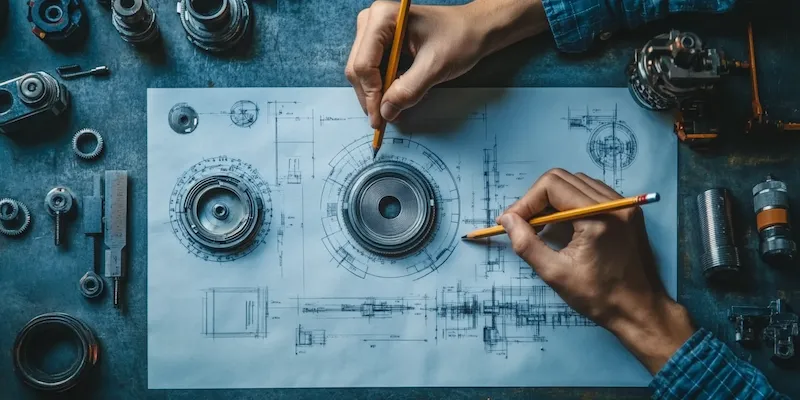
Maszyny pneumatyczne znajdują szerokie zastosowanie w wielu branżach przemysłowych dzięki swojej wszechstronności oraz efektywności działania. W przemyśle motoryzacyjnym są wykorzystywane do montażu komponentów oraz testowania części pojazdów. Dzięki precyzyjnemu sterowaniu ruchem siłowników pneumatycznych możliwe jest osiągnięcie wysokiej jakości wykonania oraz skrócenie czasu produkcji. W branży spożywczej maszyny te służą do pakowania produktów oraz transportu materiałów sypkich czy płynnych. Ich konstrukcja pozwala na zachowanie higieny oraz spełnienie norm sanitarnych wymaganych w tej dziedzinie. W przemyśle elektronicznym maszyny pneumatyczne są wykorzystywane do montażu podzespołów oraz testowania urządzeń elektronicznych. W sektorze budowlanym znajdują zastosowanie w narzędziach ręcznych, takich jak młoty udarowe czy wiertnice pneumatyczne, które ułatwiają prace budowlane i remontowe.
Jakie są najnowsze technologie w budowie maszyn pneumatycznych
W ostatnich latach rozwój technologii związanych z budową maszyn pneumatycznych znacząco wpłynął na ich efektywność oraz funkcjonalność. Nowoczesne systemy sterowania opierają się na zaawansowanych algorytmach oraz możliwościach programowania, co pozwala na precyzyjne zarządzanie procesami produkcyjnymi. Wykorzystanie technologii IoT (Internet of Things) umożliwia monitorowanie pracy maszyn w czasie rzeczywistym oraz zdalne zarządzanie ich parametrami. Dzięki temu możliwe jest szybsze wykrywanie awarii oraz optymalizacja procesów produkcyjnych. Ponadto innowacyjne materiały używane do produkcji elementów maszyn pneumatycznych przyczyniają się do zwiększenia ich trwałości oraz odporności na uszkodzenia mechaniczne i chemiczne. Wprowadzenie rozwiązań takich jak inteligentne zawory czy siłowniki z funkcjami samodiagnostyki znacznie poprawia niezawodność systemów pneumatycznych. Również miniaturyzacja komponentów sprawia, że maszyny stają się coraz bardziej kompaktowe i łatwiejsze w integracji z istniejącymi liniami produkcyjnymi.
Jakie są wyzwania związane z budową maszyn pneumatycznych
Budowa maszyn pneumatycznych, mimo licznych zalet, wiąże się także z pewnymi wyzwaniami, które mogą wpływać na ich efektywność oraz niezawodność. Jednym z głównych problemów jest konieczność zapewnienia odpowiedniej jakości sprężonego powietrza. Zanieczyszczenia, takie jak woda, olej czy cząstki stałe, mogą prowadzić do uszkodzeń komponentów oraz obniżenia wydajności systemu. Dlatego kluczowe jest stosowanie filtrów i osuszaczy, które eliminują te niepożądane substancje. Kolejnym wyzwaniem jest zarządzanie ciśnieniem w systemie. Niewłaściwe ustawienia ciśnienia mogą prowadzić do nieefektywnego działania maszyn lub ich uszkodzenia. W związku z tym konieczne jest regularne monitorowanie i kalibracja systemów pneumatycznych. Dodatkowo, ze względu na różnorodność zastosowań, projektanci muszą brać pod uwagę specyfikę każdej branży oraz dostosowywać maszyny do indywidualnych potrzeb klientów. Inżynierowie muszą również zmagać się z ograniczeniami przestrzennymi w zakładach produkcyjnych, co często wymusza innowacyjne podejście do projektowania układów pneumatycznych.
Jakie są koszty związane z budową maszyn pneumatycznych
Kiedy mówimy o budowie maszyn pneumatycznych, istotnym aspektem są koszty związane z ich zakupem oraz eksploatacją. Koszt zakupu maszyn pneumatycznych może się znacznie różnić w zależności od ich skomplikowania oraz zastosowanych technologii. Proste systemy mogą być stosunkowo tanie, jednak bardziej zaawansowane rozwiązania wymagają znacznych inwestycji. Oprócz kosztów zakupu należy uwzględnić także wydatki na instalację oraz uruchomienie systemu, które mogą być znaczące w przypadku dużych i skomplikowanych układów. Koszty eksploatacji maszyn pneumatycznych obejmują zużycie energii elektrycznej do napędu sprężarek oraz koszty związane z konserwacją i serwisowaniem urządzeń. Regularne przeglądy techniczne są kluczowe dla utrzymania sprawności systemu i zapobiegania awariom, co wiąże się z dodatkowymi wydatkami. Dodatkowo warto uwzględnić koszty materiałów eksploatacyjnych, takich jak filtry czy oleje do sprężarek.
Jakie są różnice między maszynami pneumatycznymi a hydraulicznymi
Maszyny pneumatyczne i hydrauliczne to dwa różne typy systemów napędowych, które mają swoje unikalne cechy oraz zastosowania. Główną różnicą między nimi jest medium robocze – w przypadku systemów pneumatycznych jest to sprężone powietrze, podczas gdy w hydraulicznych wykorzystuje się ciecz, najczęściej olej hydrauliczny. Ta różnica wpływa na sposób działania obu systemów oraz ich właściwości. Maszyny pneumatyczne charakteryzują się szybszym czasem reakcji oraz mniejszymi rozmiarami komponentów, co czyni je bardziej elastycznymi w zastosowaniach wymagających częstych zmian kierunku ruchu lub szybkości działania. Z drugiej strony maszyny hydrauliczne oferują większą siłę i moment obrotowy przy mniejszych rozmiarach jednostek napędowych, co czyni je idealnym rozwiązaniem w aplikacjach wymagających dużej mocy, takich jak prasy czy dźwigi. Ponadto systemy hydrauliczne są mniej podatne na zmiany temperatury otoczenia i ciśnienia atmosferycznego niż pneumatyczne, co sprawia, że są bardziej stabilne w trudnych warunkach pracy.
Jakie są przyszłościowe kierunki rozwoju technologii maszyn pneumatycznych
Przemysł 4.0 oraz rozwój technologii automatyzacji stają się kluczowymi trendami wpływającymi na przyszłość budowy maszyn pneumatycznych. W miarę jak przedsiębiorstwa dążą do zwiększenia efektywności produkcji i redukcji kosztów operacyjnych, rośnie zapotrzebowanie na inteligentne rozwiązania oparte na danych. Wprowadzenie sztucznej inteligencji oraz analizy danych pozwala na optymalizację procesów produkcyjnych poprzez przewidywanie awarii i automatyczne dostosowywanie parametrów pracy maszyn do zmieniających się warunków. Ponadto rozwój technologii IoT umożliwia integrację maszyn pneumatycznych z innymi urządzeniami w zakładzie produkcyjnym, co pozwala na stworzenie bardziej złożonych systemów automatyki przemysłowej. Również miniaturyzacja komponentów staje się istotnym trendem – mniejsze elementy pozwalają na tworzenie bardziej kompaktowych układów pneumatycznych o większej wydajności energetycznej. Warto również zwrócić uwagę na rozwój materiałów kompozytowych i nowoczesnych stopów metali, które zwiększają trwałość i odporność komponentów na uszkodzenia mechaniczne czy korozję.
Jakie są najlepsze praktyki dotyczące konserwacji maszyn pneumatycznych
Aby zapewnić długotrwałe i efektywne działanie maszyn pneumatycznych, kluczowe jest przestrzeganie najlepszych praktyk dotyczących ich konserwacji. Regularne przeglądy techniczne powinny być przeprowadzane zgodnie z zaleceniami producenta oraz harmonogramem ustalonym przez dział utrzymania ruchu w zakładzie produkcyjnym. Ważne jest również monitorowanie jakości sprężonego powietrza – filtry powinny być wymieniane zgodnie z zaleceniami producenta lub częściej w przypadku intensywnej eksploatacji systemu. Utrzymanie odpowiedniego poziomu smarowania komponentów ruchomych jest kolejnym kluczowym elementem konserwacji; niewłaściwe smarowanie może prowadzić do szybszego zużycia części oraz awarii układu. Dodatkowo warto prowadzić dokumentację wszystkich prac konserwacyjnych oraz ewentualnych napraw – pozwala to na lepsze zarządzanie cyklem życia sprzętu oraz identyfikację potencjalnych problemów zanim staną się one poważnymi awariami.