Programowanie falowników to proces, który wymaga zrozumienia zarówno teorii, jak i praktyki. Falowniki są urządzeniami elektronicznymi, które konwertują prąd stały na prąd zmienny, co pozwala na kontrolowanie prędkości i momentu obrotowego silników elektrycznych. Aby skutecznie programować falowniki, należy zacząć od zapoznania się z dokumentacją producenta, która zawiera szczegółowe informacje na temat parametrów konfiguracyjnych oraz funkcji dostępnych w danym modelu. Kluczowym krokiem jest zrozumienie podstawowych terminów, takich jak częstotliwość, napięcie, prąd oraz sposób ich regulacji. Warto również zwrócić uwagę na różne tryby pracy falownika, takie jak tryb wektora lub tryb U/f, które mogą być dostosowane do specyficznych potrzeb aplikacji. Programowanie falowników często odbywa się za pomocą specjalistycznego oprogramowania, które umożliwia łatwe wprowadzanie zmian w ustawieniach oraz monitorowanie pracy urządzenia.
Jakie są najczęstsze błędy przy programowaniu falowników?
Podczas programowania falowników wiele osób popełnia typowe błędy, które mogą prowadzić do nieefektywnej pracy urządzenia lub nawet jego uszkodzenia. Jednym z najczęstszych problemów jest niewłaściwe ustawienie parametrów dotyczących silnika, takich jak moc czy liczba biegunów. Nieprawidłowe wartości mogą prowadzić do przegrzewania się silnika lub jego niewłaściwego działania. Innym powszechnym błędem jest ignorowanie zaleceń producenta dotyczących instalacji i konfiguracji falownika. Często użytkownicy pomijają kroki związane z kalibracją lub testowaniem urządzenia przed jego uruchomieniem. Warto również pamiętać o odpowiednim podłączeniu przewodów oraz zabezpieczeniu przed zakłóceniami elektromagnetycznymi. Kolejnym istotnym aspektem jest brak monitorowania parametrów pracy falownika po jego zaprogramowaniu. Regularne sprawdzanie wartości takich jak napięcie czy prąd roboczy pozwala na szybką identyfikację ewentualnych problemów i ich rozwiązanie zanim doprowadzą one do poważniejszych awarii.
Jakie są zalety stosowania nowoczesnych falowników?
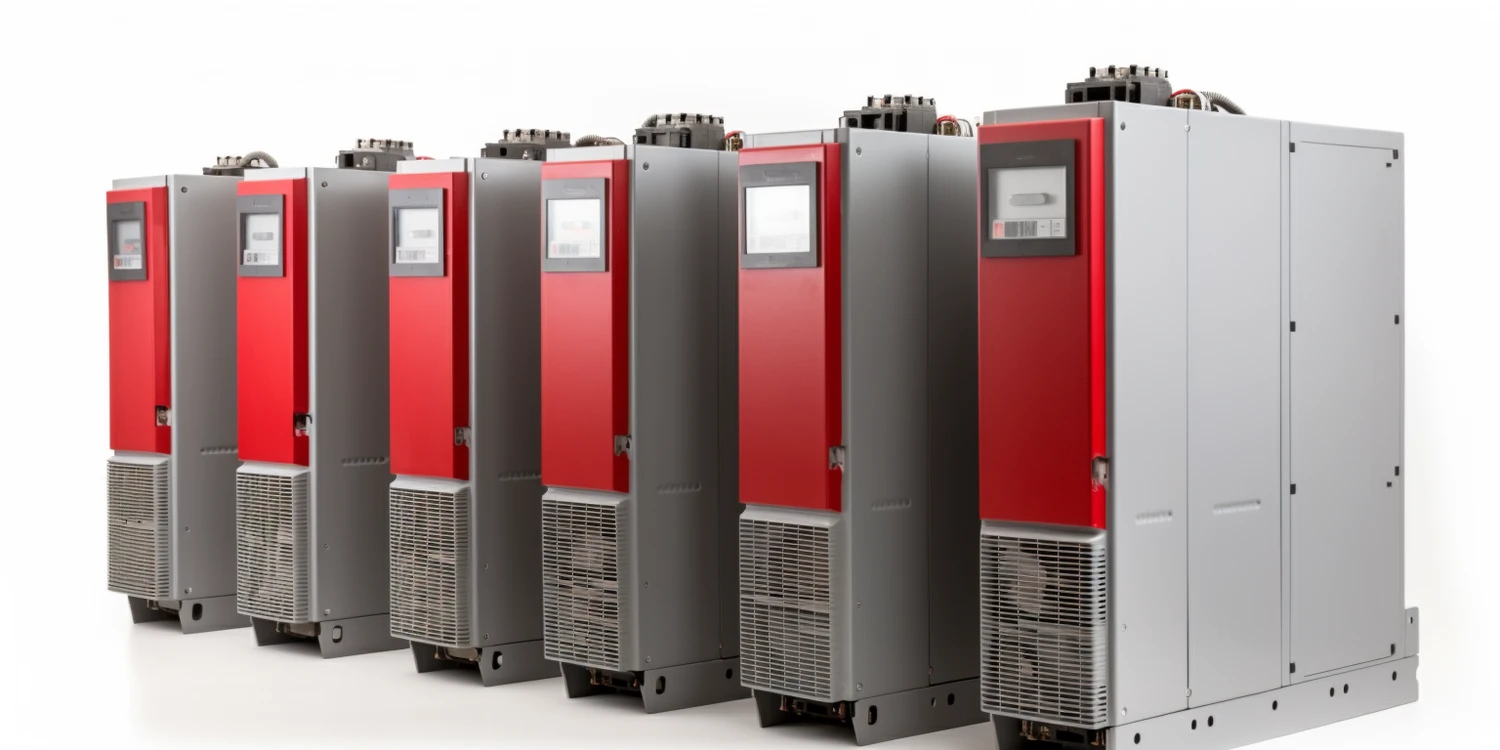
Nowoczesne falowniki oferują szereg zalet, które czynią je niezwykle atrakcyjnym rozwiązaniem w różnych aplikacjach przemysłowych i komercyjnych. Przede wszystkim umożliwiają one precyzyjne sterowanie prędkością obrotową silników elektrycznych, co przekłada się na zwiększenie efektywności energetycznej całego systemu. Dzięki zastosowaniu technologii PWM (modulacja szerokości impulsu) możliwe jest uzyskanie lepszej jakości sygnału wyjściowego oraz mniejsze straty energii. Ponadto nowoczesne falowniki często wyposażone są w zaawansowane funkcje diagnostyczne i monitorujące, co pozwala na bieżąco śledzić parametry pracy oraz szybko reagować na ewentualne problemy. Wiele modeli oferuje również możliwość komunikacji z innymi urządzeniami w systemie automatyki przemysłowej, co ułatwia integrację i zarządzanie procesami produkcyjnymi. Dodatkowo nowoczesne falowniki charakteryzują się kompaktowymi rozmiarami oraz prostą obsługą, co ułatwia ich instalację i serwisowanie.
Jakie są najważniejsze parametry do ustawienia w falownikach?
Ustawienie odpowiednich parametrów w falownikach jest kluczowe dla ich prawidłowego działania oraz efektywności energetycznej systemu. Pierwszym istotnym parametrem jest maksymalna częstotliwość wyjściowa, która definiuje maksymalną prędkość obrotową silnika. Należy ją dostosować do specyfikacji silnika oraz wymagań aplikacji. Kolejnym ważnym parametrem jest przyspieszenie i opóźnienie, które wpływają na dynamikę zmiany prędkości obrotowej silnika. Ustawienia te powinny być dobrane tak, aby zapewnić płynne działanie bez nadmiernych przeciążeń mechanicznych. Istotne są także parametry związane z ochroną silnika, takie jak limity prądowe czy zabezpieczenia przed przegrzewaniem. Falowniki często oferują możliwość ustawienia różnych trybów pracy, takich jak tryb wektora czy U/f, co pozwala na optymalizację działania w zależności od charakterystyki aplikacji.
Jakie są najlepsze praktyki przy programowaniu falowników?
Programowanie falowników wymaga nie tylko znajomości technicznych aspektów, ale również zastosowania najlepszych praktyk, które mogą znacząco poprawić efektywność i niezawodność systemu. Przede wszystkim warto rozpocząć od dokładnej analizy wymagań aplikacji, aby zrozumieć, jakie parametry będą kluczowe dla prawidłowego działania silnika. Należy również pamiętać o dokumentacji, która powinna być zawsze pod ręką, aby móc szybko odnaleźć istotne informacje dotyczące konfiguracji. Kolejną ważną praktyką jest testowanie ustawień w warunkach rzeczywistych przed pełnym wdrożeniem systemu. Dzięki temu można wychwycić ewentualne błędy i dostosować parametry do specyficznych warunków pracy. Warto także regularnie aktualizować oprogramowanie falownika, aby korzystać z najnowszych funkcji oraz poprawek bezpieczeństwa. Utrzymywanie porządku w kablach i połączeniach elektrycznych jest równie istotne, ponieważ chaotyczne okablowanie może prowadzić do zakłóceń i problemów z działaniem urządzenia.
Jakie są różnice między falownikami a innymi urządzeniami sterującymi?
Falowniki różnią się od innych urządzeń sterujących przede wszystkim swoją funkcją oraz sposobem działania. Głównym zadaniem falownika jest konwersja prądu stałego na prąd zmienny oraz kontrola prędkości obrotowej silników elektrycznych. W przeciwieństwie do prostych przekaźników czy styczników, które jedynie włączają lub wyłączają obwód, falowniki oferują zaawansowane możliwości regulacji oraz monitorowania parametrów pracy silnika. Dodatkowo falowniki pozwalają na płynne sterowanie prędkością obrotową, co jest kluczowe w wielu aplikacjach przemysłowych, gdzie precyzyjna kontrola jest niezbędna. Inną różnicą jest to, że falowniki często integrują funkcje diagnostyczne i zabezpieczające, co pozwala na szybsze wykrywanie problemów oraz automatyczne reagowanie na awarie. Warto również zauważyć, że nowoczesne falowniki mogą komunikować się z innymi urządzeniami w systemie automatyki przemysłowej poprzez różne protokoły komunikacyjne, co umożliwia ich łatwą integrację w bardziej złożonych systemach.
Jakie są najczęstsze zastosowania falowników w przemyśle?
Falowniki znajdują szerokie zastosowanie w różnych branżach przemysłowych ze względu na swoją zdolność do precyzyjnego sterowania silnikami elektrycznymi. Jednym z najczęstszych zastosowań jest kontrola napędów w systemach transportowych, takich jak taśmy transportowe czy podajniki. Dzięki możliwości regulacji prędkości obrotowej falowniki pozwalają na optymalizację procesów transportowych oraz zwiększenie efektywności energetycznej. Innym popularnym zastosowaniem jest automatyka budynkowa, gdzie falowniki są używane do sterowania wentylatorami, pompami czy klimatyzacją. W takich aplikacjach ich zdolność do płynnej regulacji prędkości przekłada się na oszczędności energii oraz komfort użytkowników. Falowniki wykorzystywane są także w przemyśle motoryzacyjnym do sterowania silnikami elektrycznymi w pojazdach hybrydowych i elektrycznych. W sektorze produkcyjnym falowniki odgrywają kluczową rolę w automatyzacji procesów produkcyjnych poprzez kontrolę maszyn CNC czy robotów przemysłowych.
Jakie są koszty związane z zakupem i eksploatacją falowników?
Koszty związane z zakupem i eksploatacją falowników mogą się znacznie różnić w zależności od ich typu, mocy oraz dodatkowych funkcji. Przy zakupie falownika należy uwzględnić nie tylko cenę samego urządzenia, ale także koszty instalacji oraz ewentualnych akcesoriów potrzebnych do jego prawidłowego działania. Warto również rozważyć długoterminowe koszty eksploatacji, takie jak zużycie energii elektrycznej oraz koszty serwisowania i konserwacji. Falowniki charakteryzują się wysoką efektywnością energetyczną, co może prowadzić do znacznych oszczędności w dłuższym okresie użytkowania. Należy jednak pamiętać o regularnym monitorowaniu ich pracy oraz przeprowadzaniu konserwacji, aby uniknąć kosztownych napraw czy wymiany sprzętu. Dodatkowo warto zwrócić uwagę na dostępność części zamiennych oraz wsparcia technicznego ze strony producenta lub dostawcy.
Jakie są przyszłe trendy w technologii falowników?
Przemysłowy rynek falowników stale ewoluuje, a przyszłe trendy wskazują na dalszy rozwój technologii związanej z tymi urządzeniami. Jednym z najważniejszych kierunków rozwoju jest integracja sztucznej inteligencji oraz uczenia maszynowego w systemach sterujących falownikami. Dzięki tym technologiom możliwe będzie bardziej zaawansowane monitorowanie parametrów pracy oraz automatyczne dostosowywanie ustawień do zmieniających się warunków operacyjnych. Kolejnym trendem jest rosnąca popularność rozwiązań opartych na energii odnawialnej, takich jak panele słoneczne czy turbiny wiatrowe, które wymagają zaawansowanych systemów zarządzania energią i integracji z siecią energetyczną. Falowniki będą odgrywać kluczową rolę w tych systemach jako elementy konwertujące energię z różnych źródeł na formę użyteczną dla odbiorców końcowych. Dodatkowo obserwuje się wzrost zainteresowania rozwiązaniami IoT (Internet of Things), które umożliwiają zdalne monitorowanie i zarządzanie pracą falowników przez internet.
Jakie są wyzwania związane z programowaniem i użytkowaniem falowników?
Programowanie i użytkowanie falowników wiąże się z wieloma wyzwaniami, które mogą wpływać na ich skuteczność oraz niezawodność działania. Jednym z głównych wyzwań jest konieczność ciągłego dostosowywania ustawień do zmieniających się warunków operacyjnych oraz specyfikacji aplikacji. W miarę jak technologie się rozwijają i pojawiają nowe wymagania dotyczące wydajności i efektywności energetycznej, operatorzy muszą być gotowi do regularnego aktualizowania swoich umiejętności oraz wiedzy na temat programowania falowników. Kolejnym wyzwaniem jest integracja falowników z innymi systemami automatyki przemysłowej, co może wymagać zaawansowanej wiedzy technicznej oraz umiejętności programistycznych. Problemy związane z kompatybilnością różnych protokołów komunikacyjnych mogą prowadzić do trudności w integracji urządzeń i wymagać dodatkowego czasu oraz zasobów na ich rozwiązanie. Ponadto operatorzy muszą być świadomi zagrożeń związanych z bezpieczeństwem danych oraz cyberatakami, które mogą wpłynąć na działanie systemu automatyki przemysłowej.